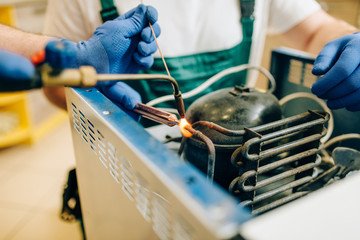
Commercial freezers see a lot of use. They’re frequently accessed, especially in busy restaurants, and they take a beating on their doors, hinges, cooling units, and more.
If your commercial freezer shows signs of aging, like temperature issues or leaks, contact Sub Zero Repair Seattle immediately.
1. Water Leaks
Leaks in commercial freezers often signal problems with the unit’s components. The drain lines, defrost system, and door gasket can all become damaged or clogged with debris over time, which allows warm air to enter the freezer and cause excessive condensation. This can lead to food and liquor spoilage, which may result in significant business losses for the owner. Water leaks inside or around the freezer are also a sign of an issue with the compressor, which is responsible for cooling the unit. These issues could be due to electrical failure, refrigerant leaks, or general wear and tear.
Commercial freezers require regular cleaning and monitoring to avoid malfunctions. Taking precautionary measures like keeping the freezer clean and addressing temperature inconsistencies can prevent costly repairs in the future. By recognizing early warning signs and scheduling routine maintenance, owners can extend the lifespan of their commercial freezers.
Commercial freezers are vital for businesses that depend on them for storage and preservation of valuable products. Identifying potential commercial freezer problems and seeking professional help promptly can reduce product loss and protect a company’s reputation. Using the right tools for freezer maintenance and understanding common problem indicators will help minimize breakdowns and reduce energy consumption, making it easier to keep costs low and productivity high. To learn more about reducing commercial freezer repair costs, contact the experts at Comfort Boys for comprehensive services and maintenance plans. Their expert technicians will thoroughly clean and inspect your commercial freezers, ensuring all components are functioning properly and efficiently. They can also help you develop a preventive maintenance plan that includes tasks like testing temperature controls, cleaning coils, and lubricating moving parts.
2. Inconsistent Temperature
Commercial freezers and walk-in coolers play a vital role for food-related businesses, as they ensure that products stay fresh and safe to eat. However, when these appliances break down or start to show signs of trouble, it can be detrimental to the entire operation. Not only does it lead to spoiled food, but it can also increase energy bills and cause other issues. That’s why it’s important to pay attention to the signs that your commercial freezer is going bad, so you can get it repaired before it’s too late.
One of the most common issues with a commercial freezer is inconsistent temperatures. While a slight variation is normal, drastic fluctuations in temperature could indicate that there’s something wrong with the compressor or thermostat. It’s imperative to call a technician as soon as possible to determine what the issue is and fix it before it becomes worse.
Another sign that your commercial freezer is in need of repair is when it starts to leak. This can happen due to a number of different reasons, including worn seals or an improper installation. In any case, it’s important to have the problem fixed as quickly as possible, as standing water poses several health hazards and can cause costly damage to the equipment and contents inside the freezer.
A leaking freezer can also lead to problems with the temperature control. This happens because the cold air can escape the freezer and warm air can seep in, causing the temperature to rise. Regularly checking the door seals and cleaning the coils (if applicable) is a good way to prevent this from happening. You can usually access the coils by removing the freezer’s grille, so it’s easy to do on a regular basis.
3. Strange Sounds
Commercial refrigerators are not exactly known for being silent machines, and they can make quite a lot of noise as they operate. However, some sounds are normal and nothing to worry about, while others can be a sign that something is wrong with the unit.
For instance, a humming sound is typical as the freezer is running, and this is the result of the compressor working to circulate refrigerant through the evaporator coil to remove heat. On the other hand, a clicking or banging sound may indicate that the fan isn’t turning correctly, which can cause your freezer to not cool properly.
In addition, a rattling sound can be an indication that something is loose inside the freezer. This could be anything from a fan blade to the compressor itself, so this is definitely a problem that should be addressed immediately.
Finally, if you hear strange popping or crackling sounds coming from your freezer, it’s likely due to the walls expanding and contracting as they change temperature. While this isn’t an emergency, it should still be looked at by a professional.
The best way to keep your freezer in top condition is with regular preventive maintenance services. Quick Servant offers customizable maintenance programs that can help you save money and extend the life of your equipment by cleaning evaporator coils, calibrating thermometers, checking compressor pressures, lubricating door hinges, and more.
4. High Energy Bills
Commercial freezers and walk-in coolers use a lot of energy to keep food at an optimal temperature. If they’re working overtime, it can significantly increase your utility bills. You should check your energy bill regularly to see if you spot any sudden spikes. Also, you can take measures to lower your energy bills, such as replacing the door gaskets to prevent cold air leakage, cleaning the condenser coils and evaporator to ensure efficient heat dissipation, and lubricating fan motors and other moving parts to reduce friction.
Regular inspections can help your freezer save energy and extend its lifespan. An inspector can look for signs of a broken thermostat or faulty controls, and can recommend repairs or replacements. In addition, state-of-the-art freezer motors demand less electricity than older models and run quieter, which can greatly cut your energy bill. In fact, if you’re frequently calling in emergency freezer repair services, it might be worth investing in a new freezer with a better warranty and more efficient operating costs.
Keeping your commercial freezer running smoothly can have a positive impact on your business operations. It can prevent product loss and ensure compliance with strict food safety standards. It can also make it easier to keep your customers happy by providing them with a reliable supply of fresh products.
But when your walk-in freezer stops functioning properly, you have a dilemma. Do you invest in commercial freezer repair or purchase a new unit?
5. Damaged Door Gasket
Commercial freezers can be a lifeline for many restaurants and businesses, protecting thousands of dollars in inventory. However, as with any equipment, proper maintenance is key to maintaining efficiency and longevity. A faulty freezer can result in lost inventory, financial losses, and a negative reputation for your business. Keep an eye out for these warning signs to schedule commercial freezer repair before the problem escalates.
Water leaks inside or around your freezer are an indication of a clogged drain line, malfunctioning defrost system, or damaged door gasket. These problems should be dealt with immediately to prevent water damage and protect food quality.
Poor-fitting or damaged gaskets allow warm air to circulate past the insulated doors, creating an ideal breeding ground for bacteria. This creates a health hazard for employees and customers while also forcing the compressor to work harder, increasing your energy bills.
If you notice that your gasket is leaking, this means that it’s time to replace it. Depending on the type of gasket, you may need to clean it and remove any food debris before installing a new one. If your gasket is twisted or warped, try placing it in hot water for 30 minutes to straighten out the kinks. It’s important not to heat it up too much, as this could melt the plastic and compromise its durability. Once the gasket has cooled, remove it and wipe down the channel to make sure that there is no residue from previous adhesive installations. Finally, use silicone grease or petroleum jelly to fill any small gaps in the seal. Make sure the adhesive is well-coated before closing the refrigerator door. If the gap is large enough, you can use a strip of wax paper to cover it.